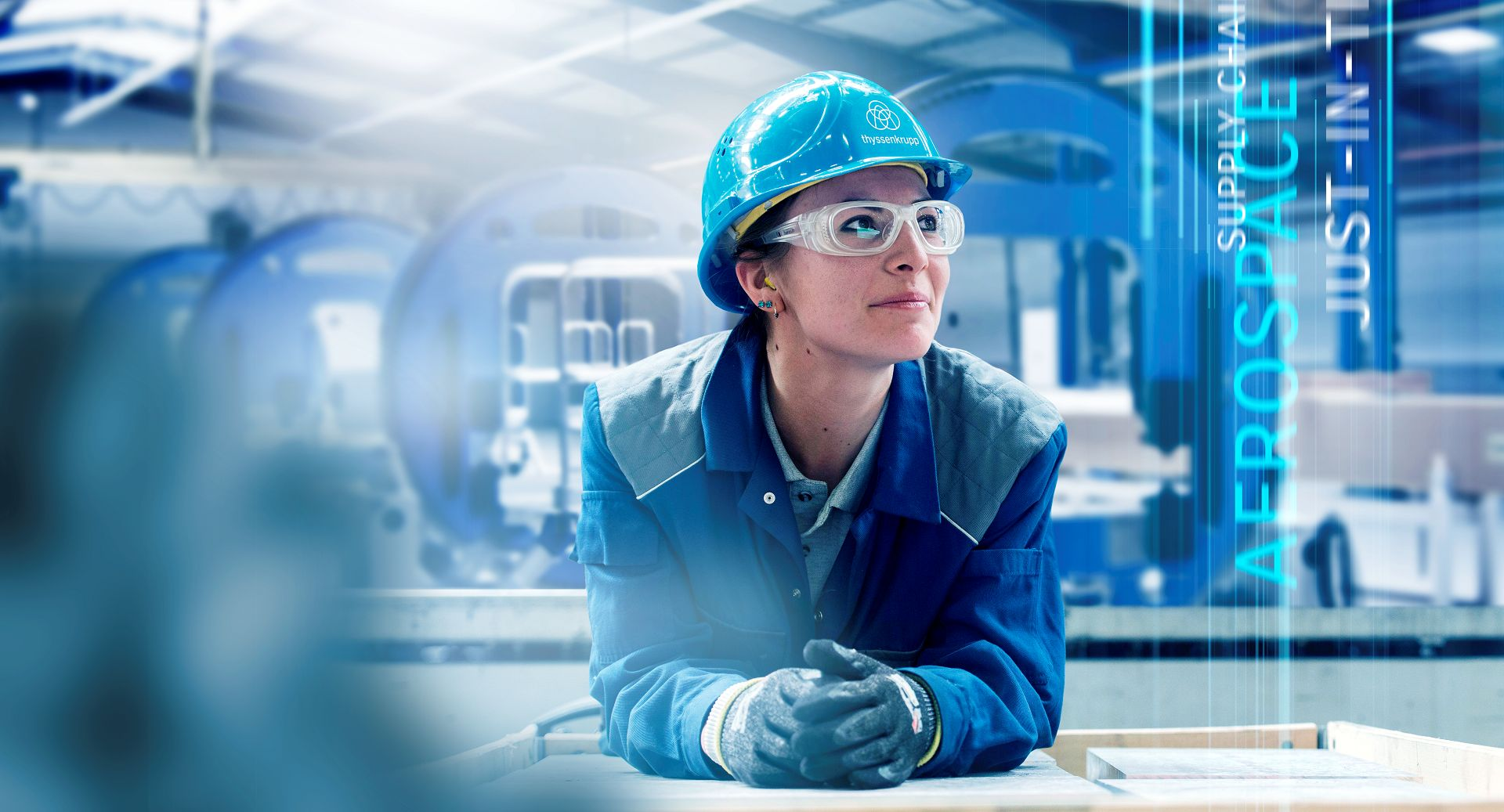
As one of the world's leading supply chain management and 3PL service providers in the market for raw materials, thyssenkrupp Aerospace offers end-to-end solutions to build resilient and digital supply chains.
Learn more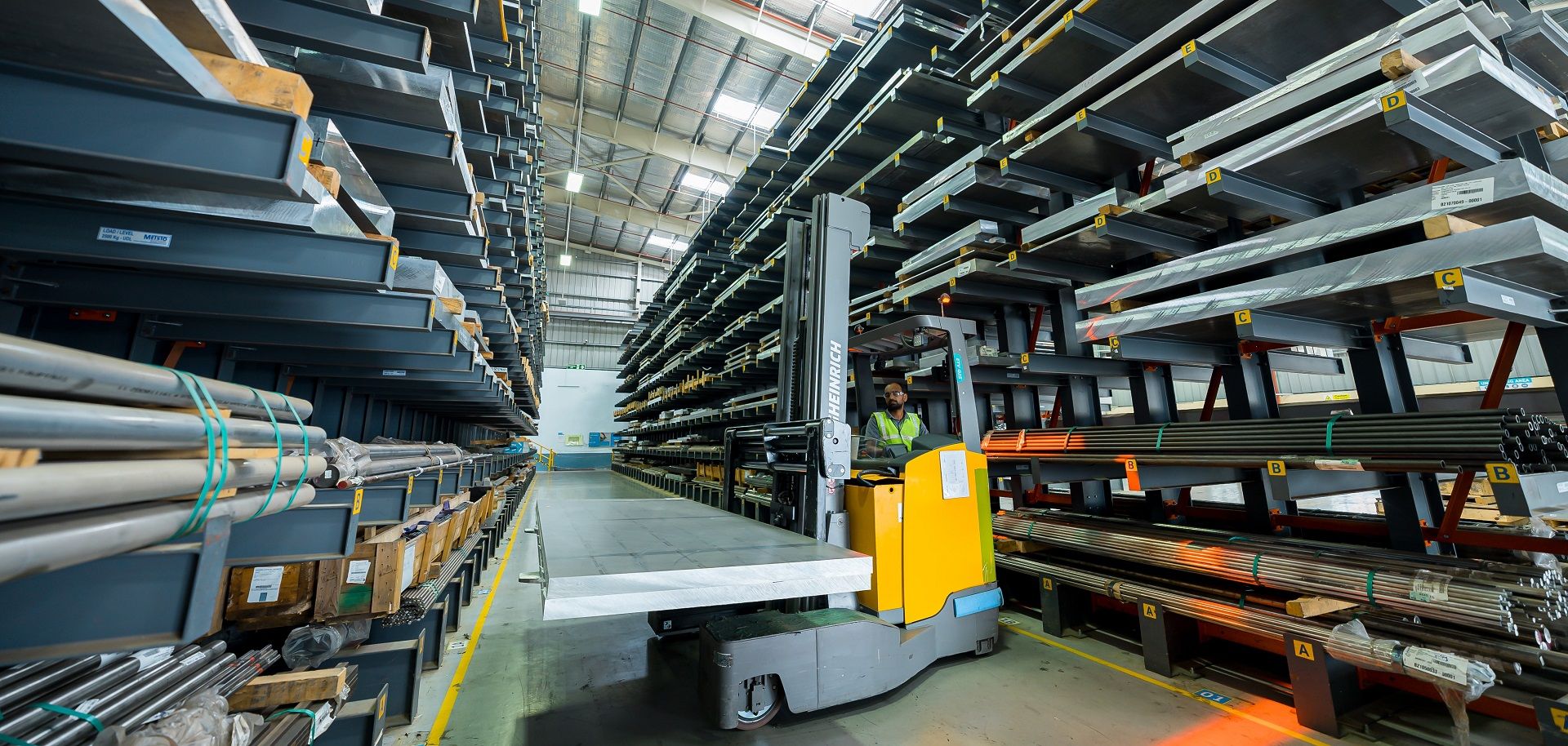
Whether it is aluminum, titanium, steel, special alloys or aerospace plastics, we stock a full range of the materials used for building aircraft in standard sizes or cut-to-specification. And with a local presence in over 40 locations and 20 countries, we guarantee security of supply. Our range of flexible services can also help to reduce your procurement costs and streamline your inventory.
Learn more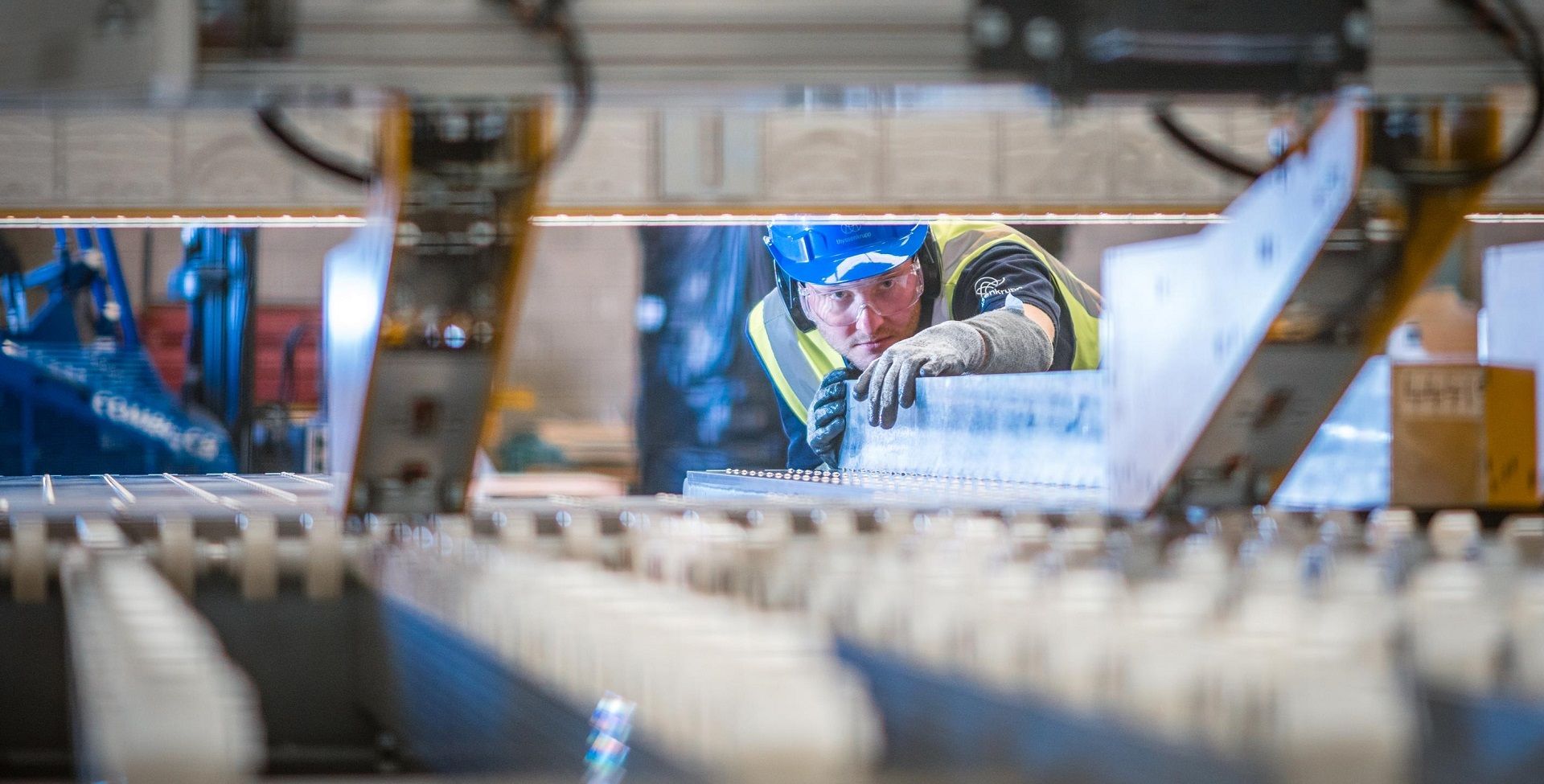
Modern aircraft are assembled with high-precision materials. We are the industry leaders when it comes to supplying these materials. Cut exactly to specification and delivered just-in-time, we are one of the first links in a long chain that transforms metal alloys into finished aircraft components.
Learn more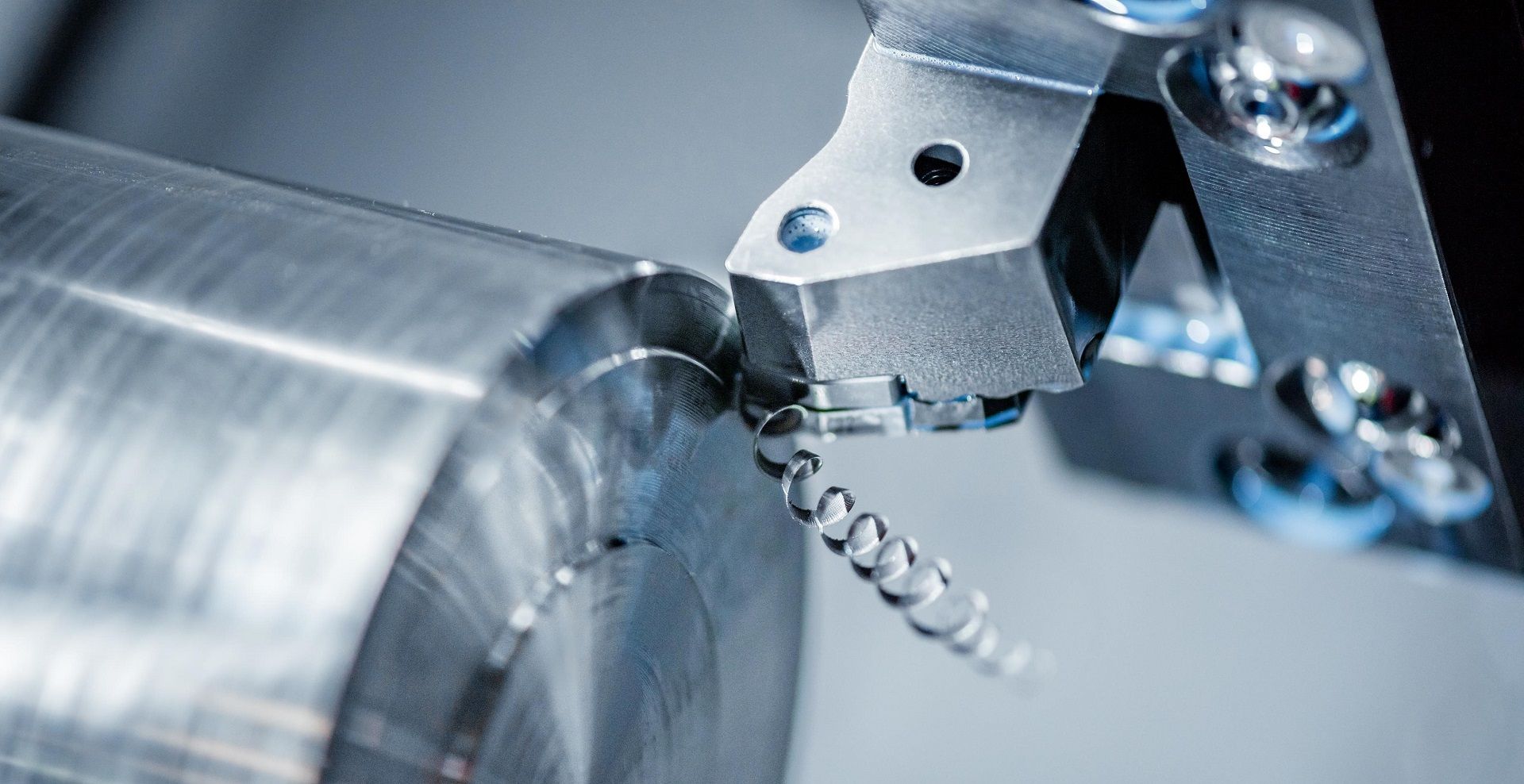
thyssenkrupp Aerospace is partner of choice for many ambitious customers in the industry. In addition to our unrivalled machining services, we remove process bottlenecks by eliminating redundant in-house inspection and testing. This leads to considerable time savings and cost reductions.
Learn more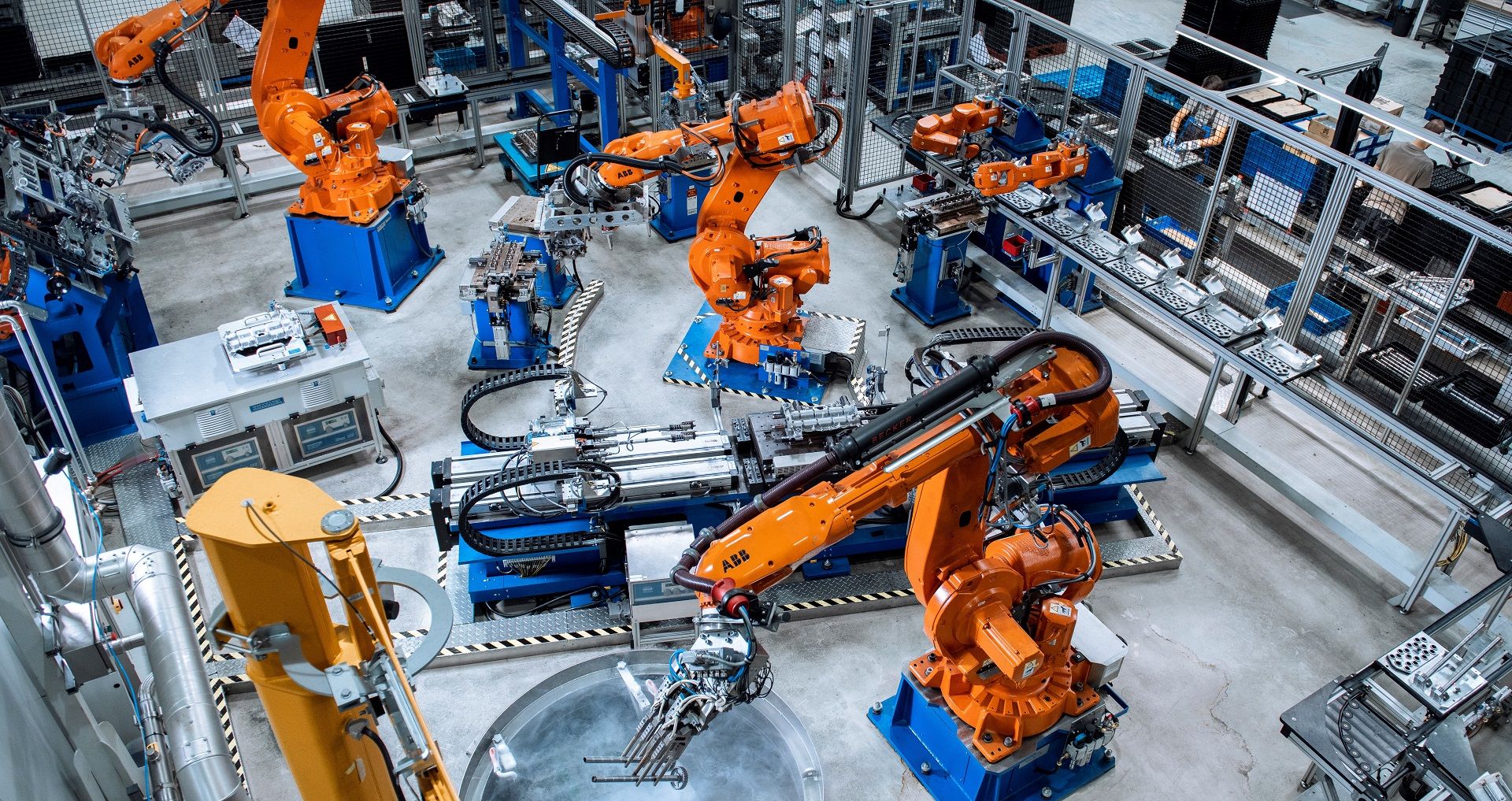
Our commitment to reshaping the material supply chain will bring several welcome benefits to our customers, including secure supplies, reduced logistics costs, improved information flows and more efficiency.
Learn more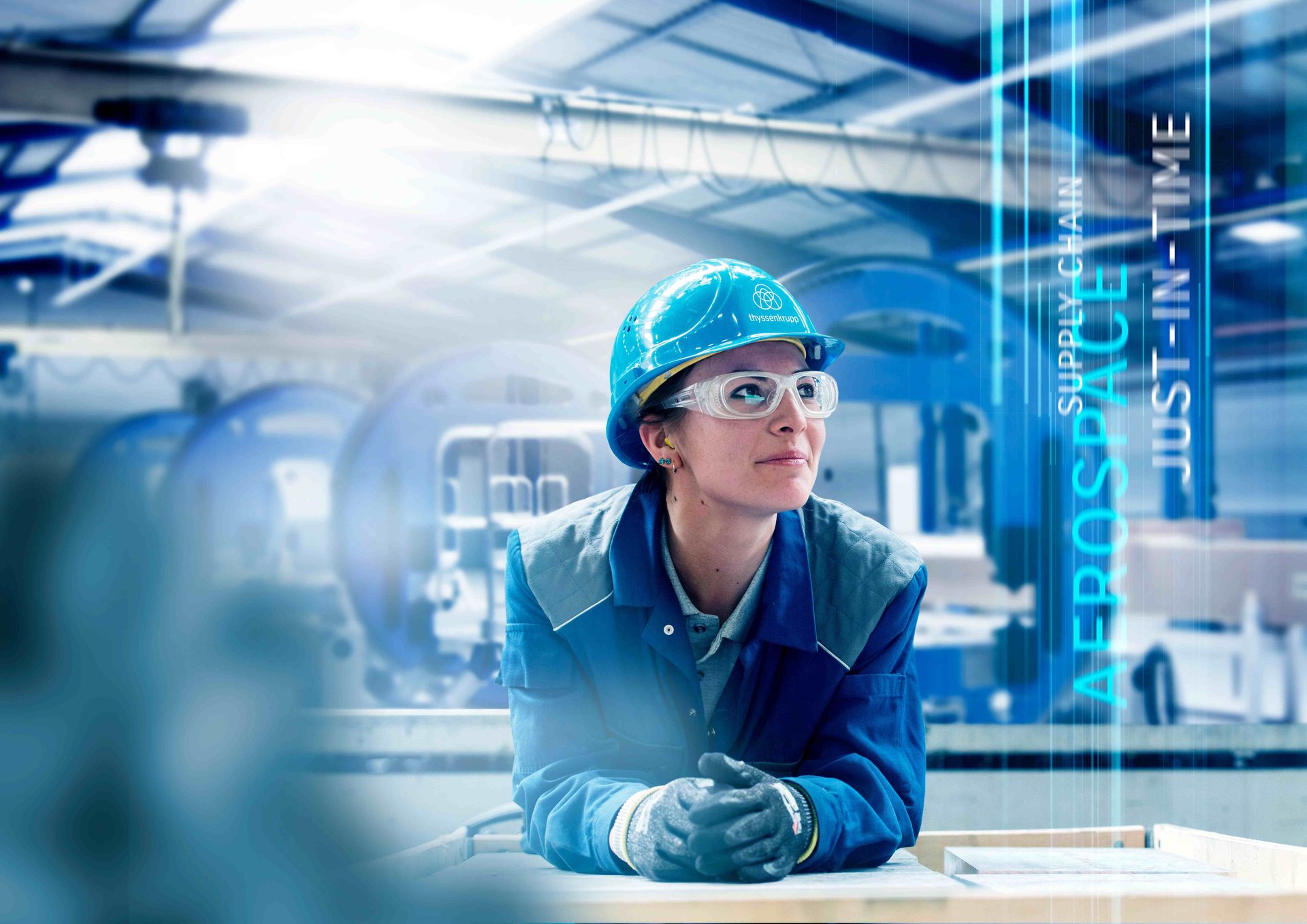
As one of the world's leading supply chain management and 3PL service providers in the market for raw materials, thyssenkrupp Aerospace offers end-to-end solutions to build resilient and digital supply chains.
Learn more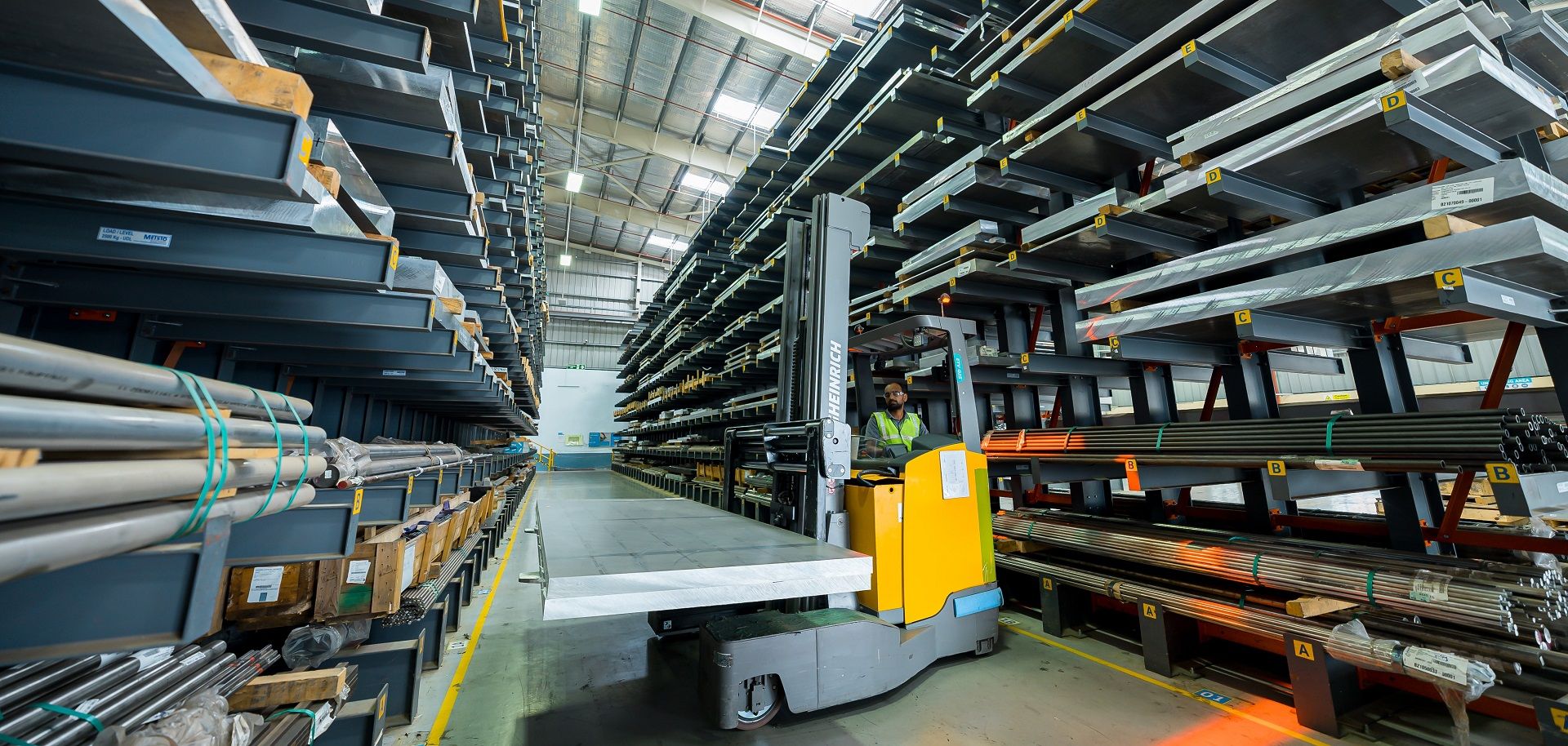
Whether it is aluminum, titanium, steel, special alloys or aerospace plastics, we stock a full range of the materials used for building aircraft in standard sizes or cut-to-specification. And with a local presence in over 40 locations and 20 countries, we guarantee security of supply. Our range of flexible services can also help to reduce your procurement costs and streamline your inventory.
Learn more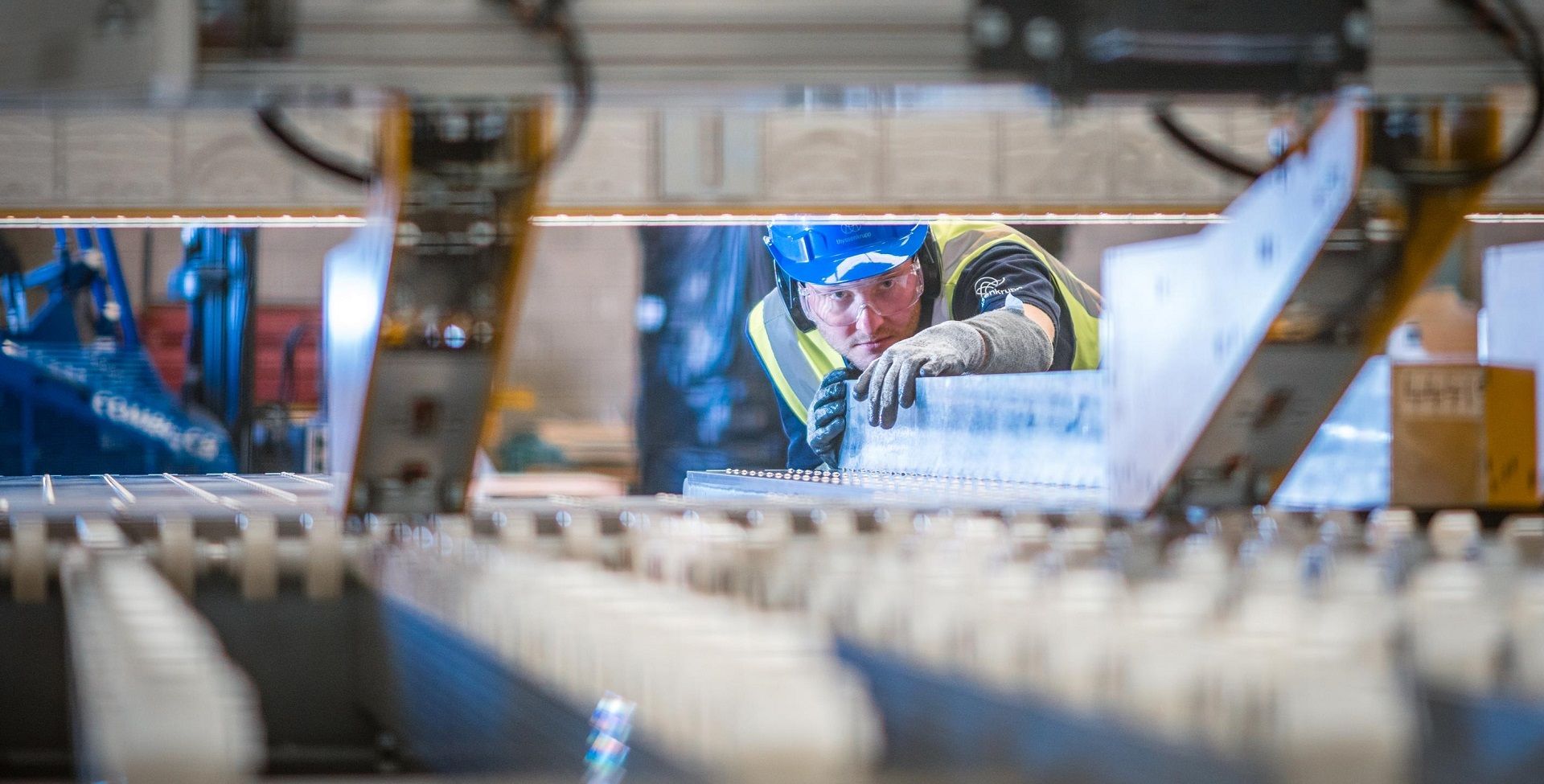
Modern aircraft are assembled with high-precision materials. We are the industry leaders when it comes to supplying these materials. Cut exactly to specification and delivered just-in-time, we are one of the first links in a long chain that transforms metal alloys into finished aircraft components.
Learn more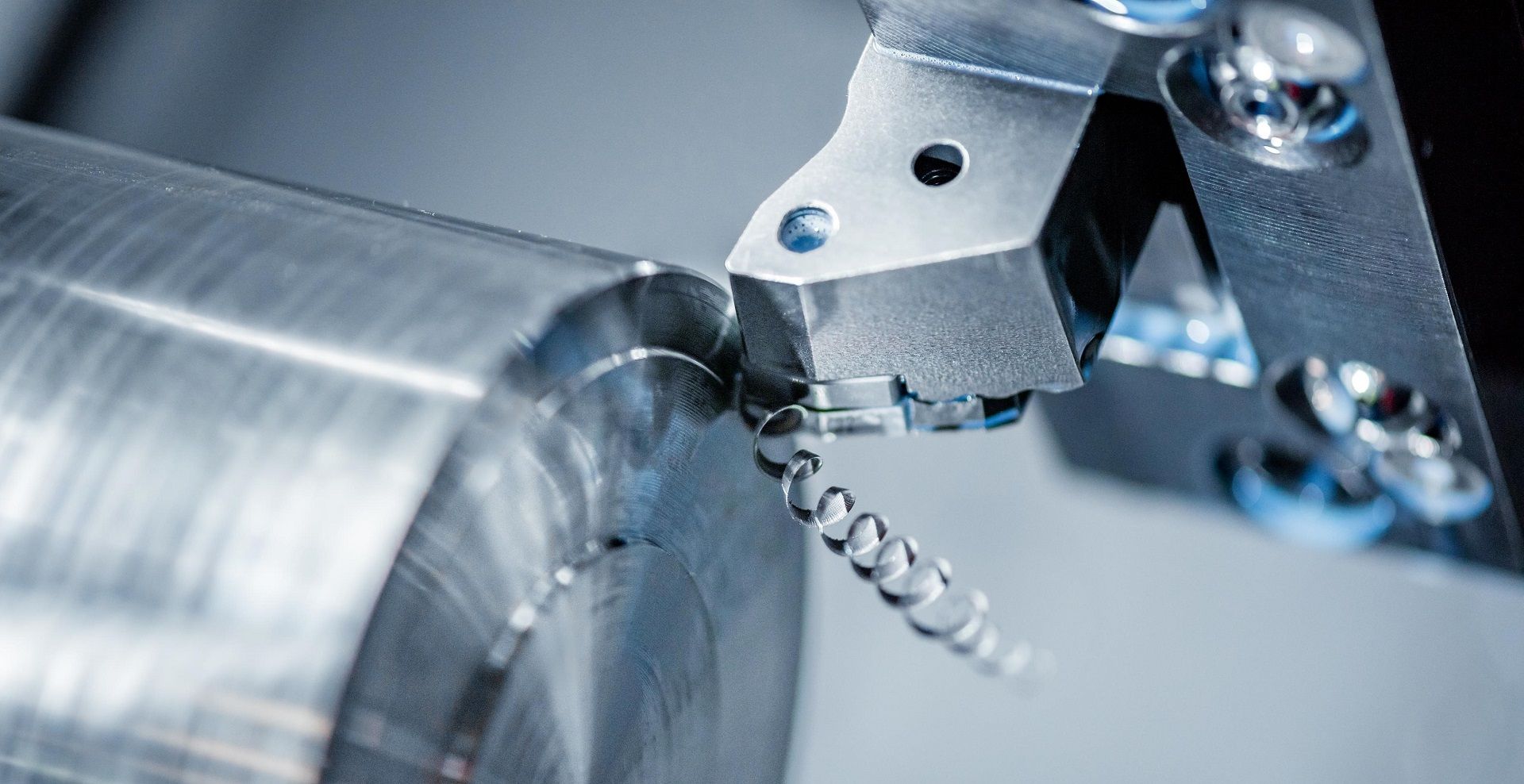
thyssenkrupp Aerospace is partner of choice for many ambitious customers in the industry. In addition to our unrivalled machining services, we remove process bottlenecks by eliminating redundant in-house inspection and testing. This leads to considerable time savings and cost reductions.
Learn more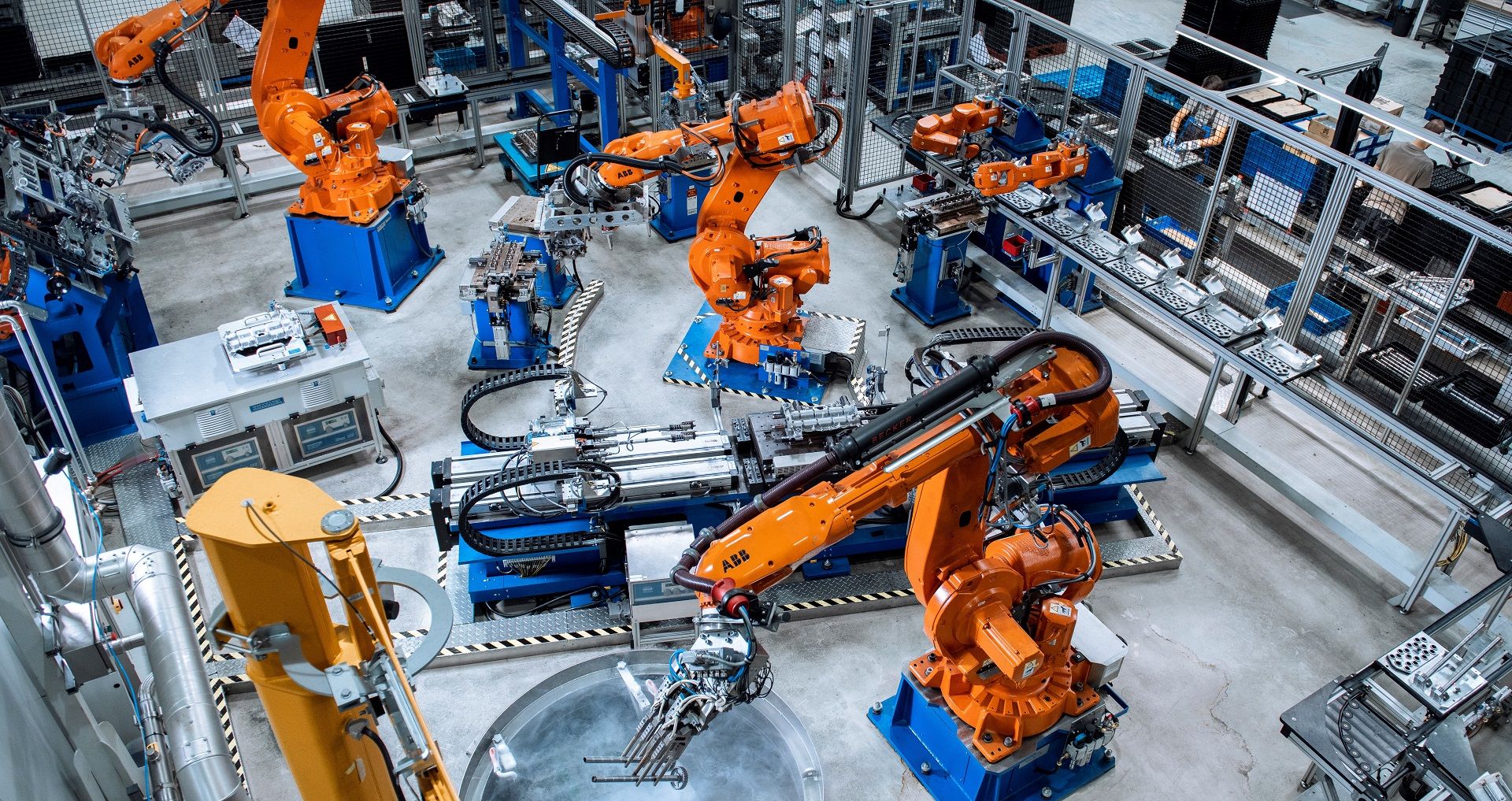
Our commitment to reshaping the material supply chain will bring several welcome benefits to our customers, including secure supplies, reduced logistics costs, improved information flows and more efficiency.
Learn moreMaterials
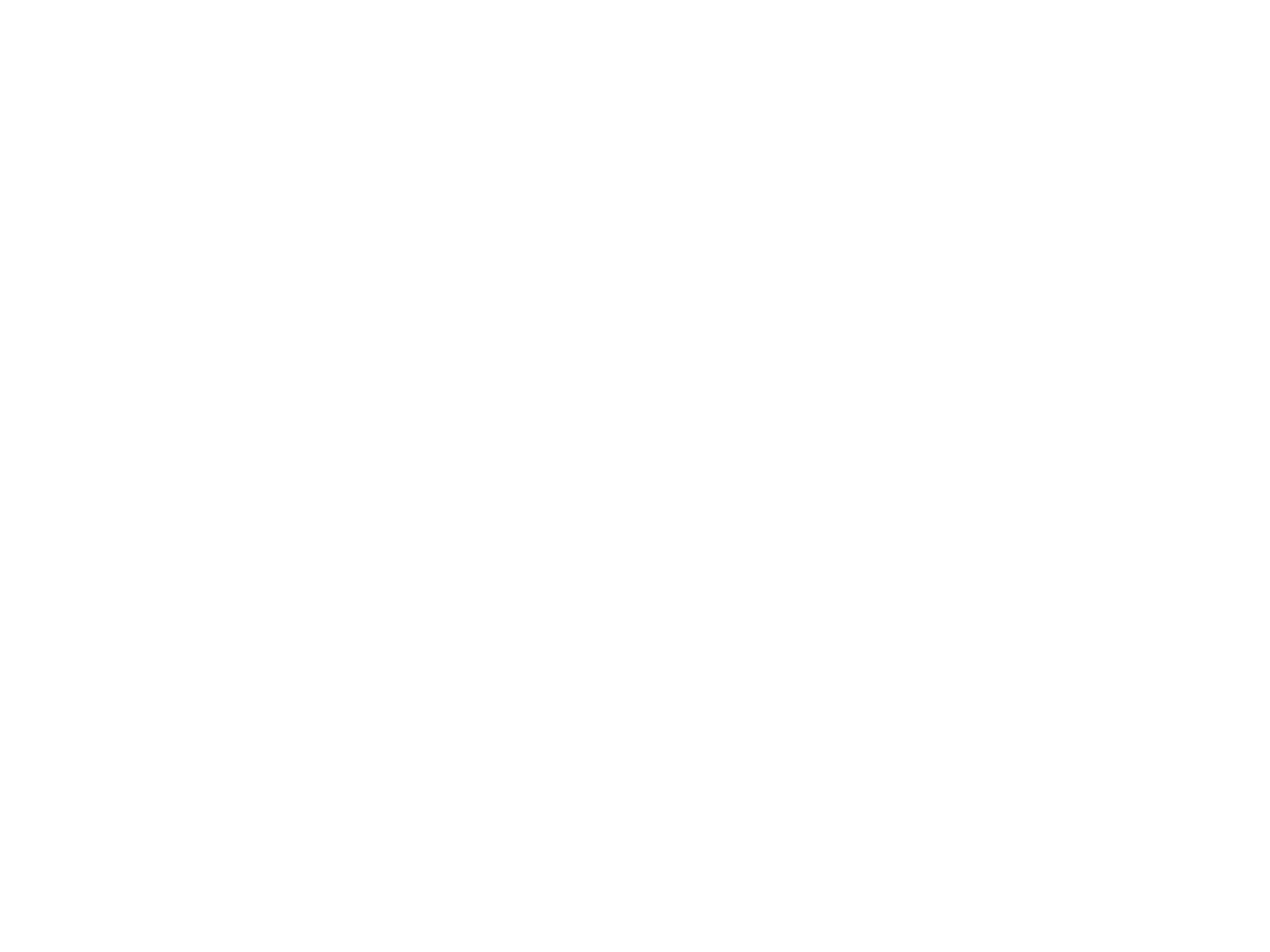
Aluminum offers corrosion resistance and a high strength-to-weight ratio. This makes it easier for aircraft to reach a flight speed of around 900km/h while keeping fuel consumption low.
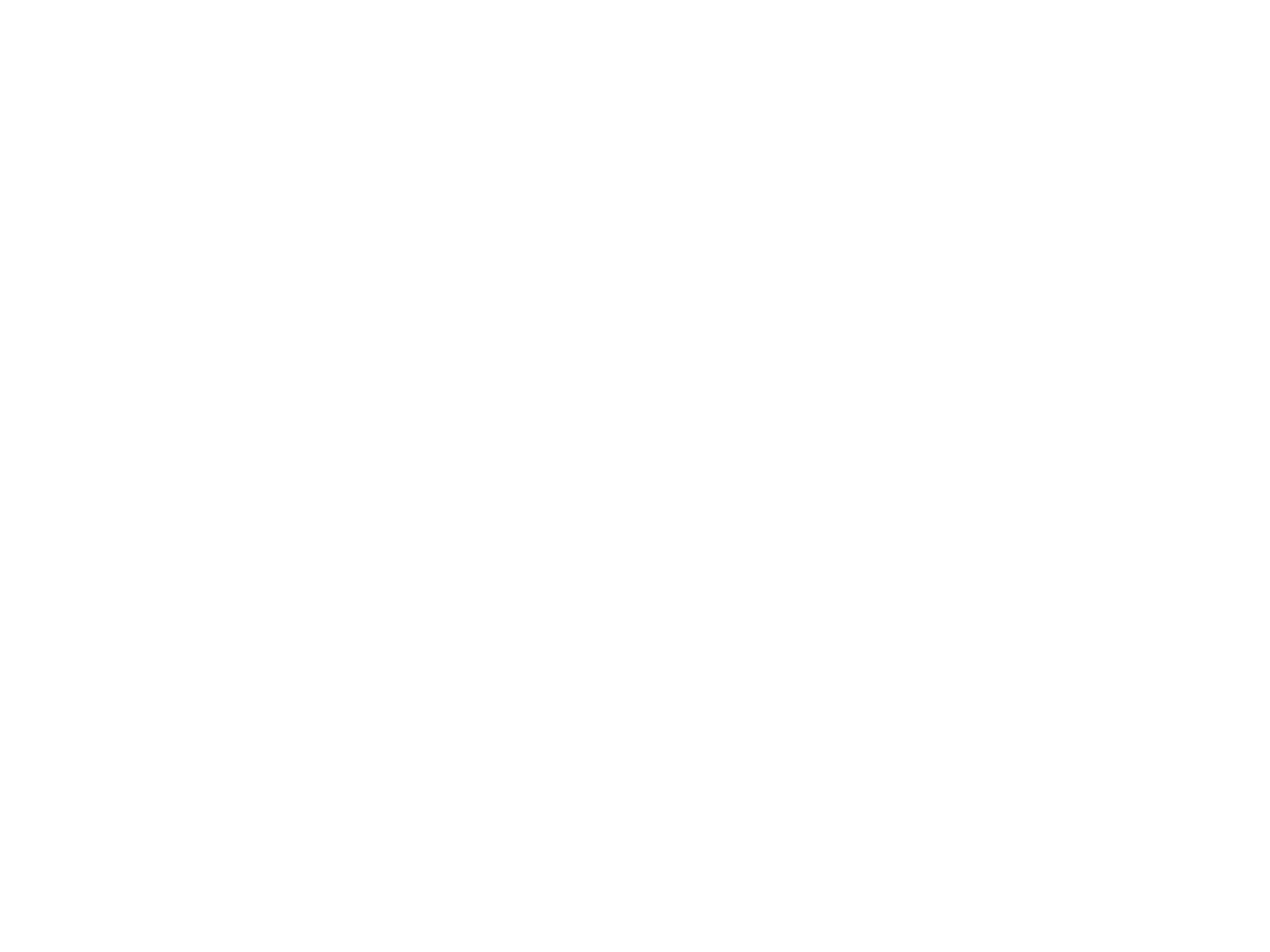
As the largest materials distributor in the Western hemisphere, we guarantee the supply of this vital metal for our customers. Through expert advice, reliability, and a large stock of materials, we make sure our clients get their materials just-in-time wherever they need it.
Find out moreProcessing Services
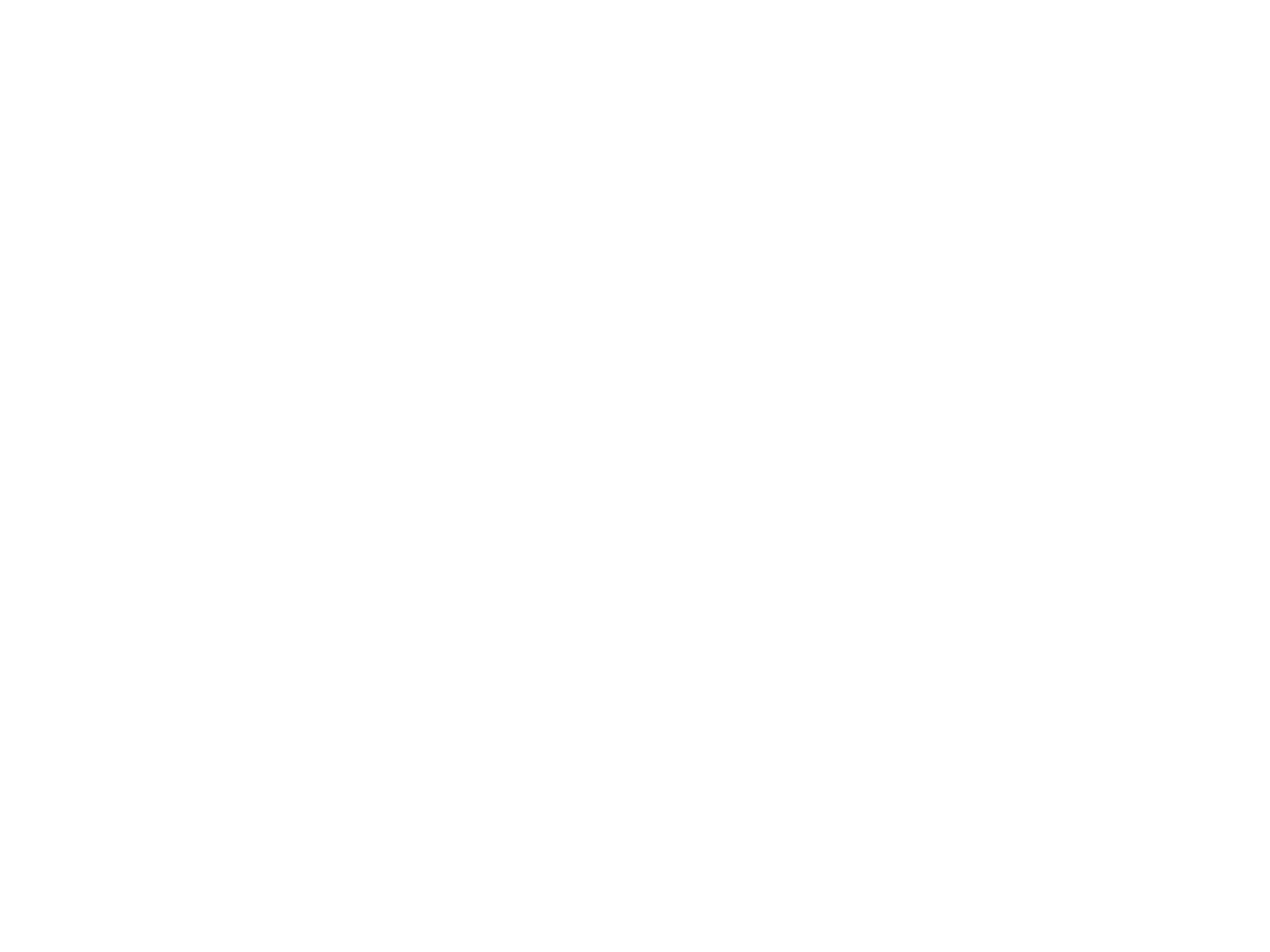
The so-called buy-to-fly ratio indicates the ratio between material inputs and outputs. In the aerospace industry, the majority of the materials acquired to make an aircraft end up as scrap. This is the result of inefficient processes along the supply chain and poor forecasting.
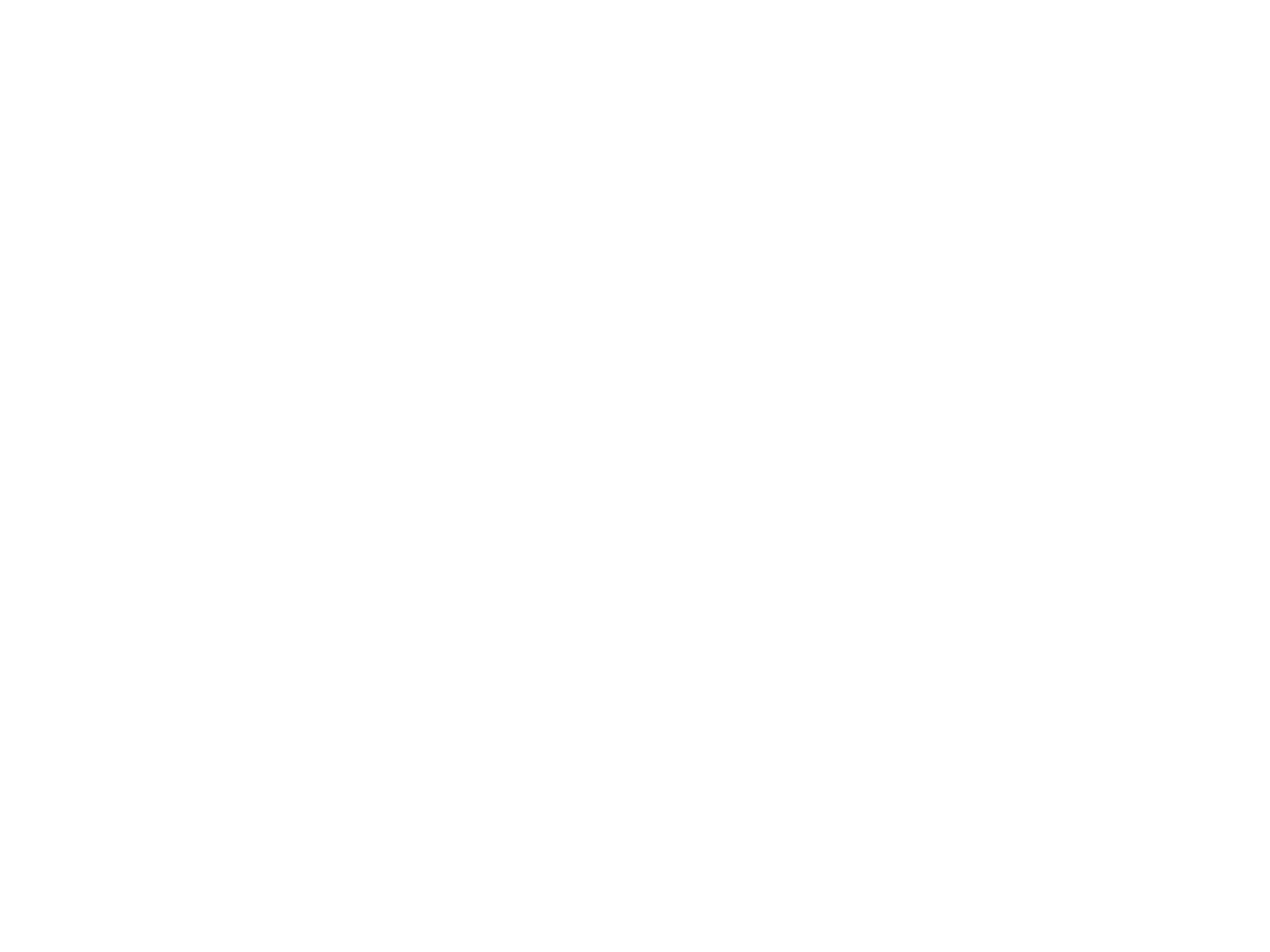
At thyssenkrupp Aerospace, our objectives are always to maximize quality and minimize scrap in all our processing services. By using smart processes such as nesting, we aim to keep your costs low, the quality of our materials high, and environmental impacts as low as possible.
Find out moreMachining
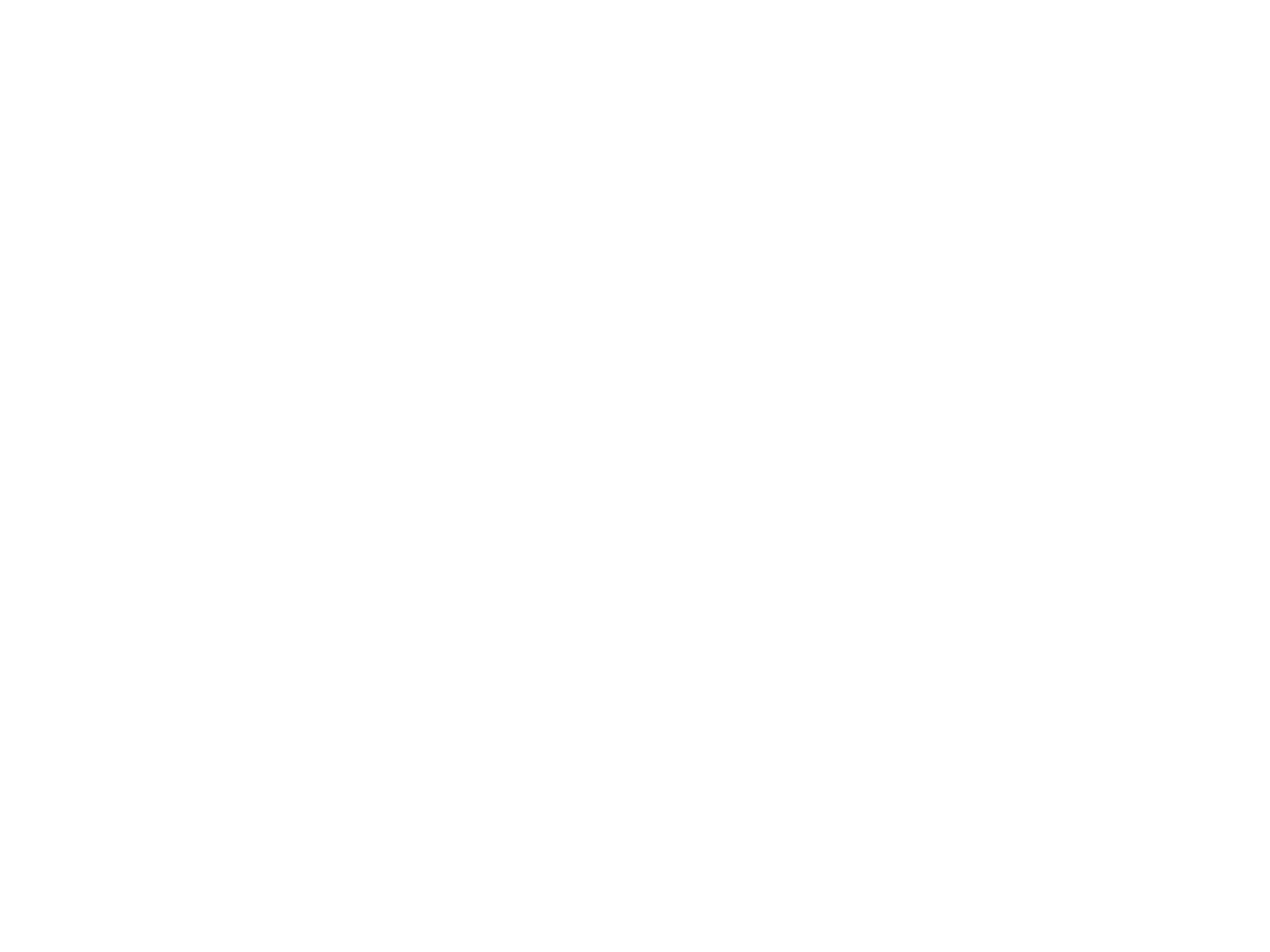
The aerospace industry works to the highest standards when it comes to processed materials. These materials operate under extreme conditions so the tolerances used in their manufacture are more precise than in almost any other industry.
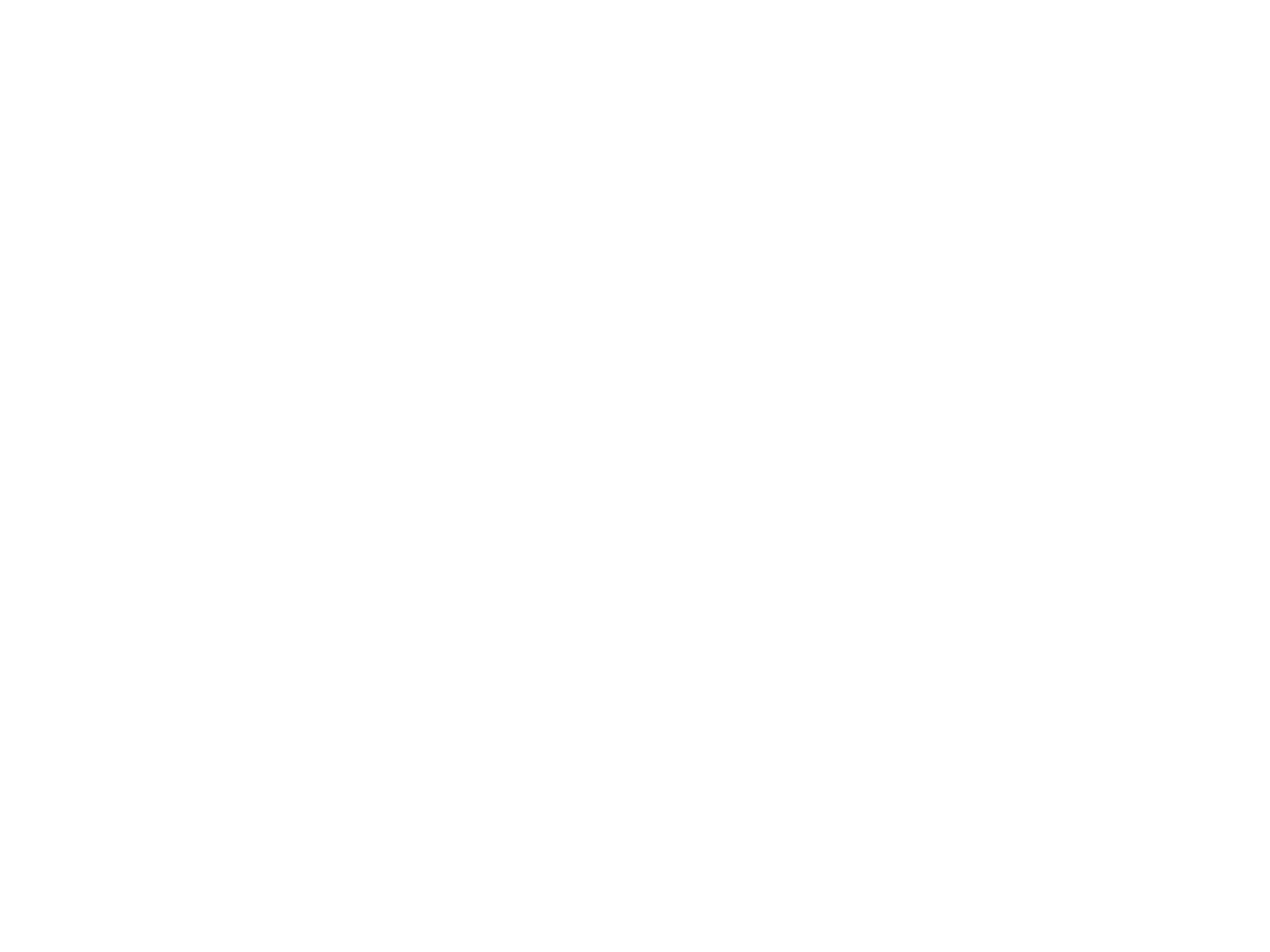
Our customers save time and effort by putting the pre-machining of their materials into our expert hands. We work to highest engineering standards and use state-of-the-art machines. By focusing on their core business and leaving processing services to us, our customers stay competitive in their core business.
Find out moreSupply Chain Management
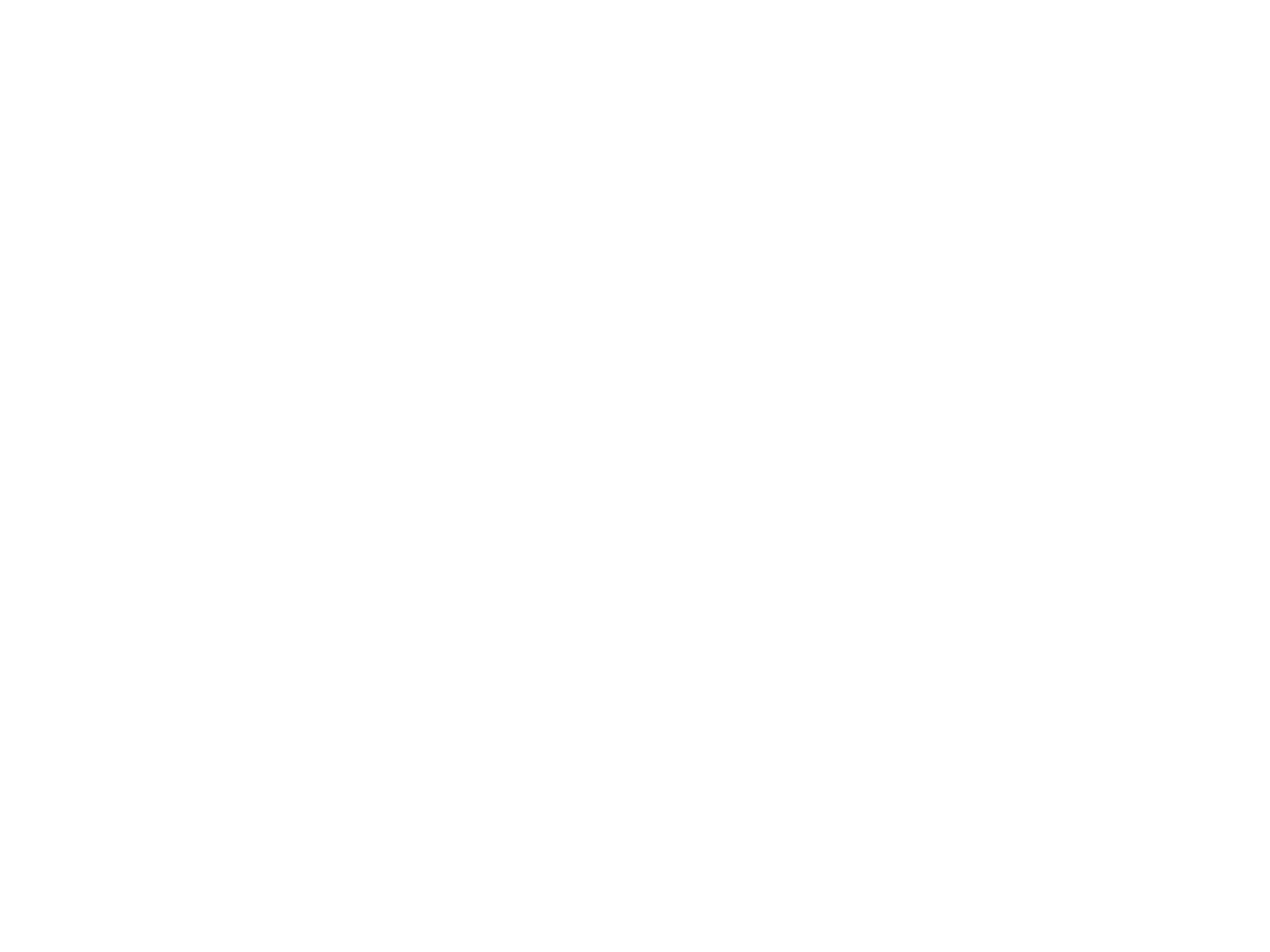
A large airplane consists of up to 6,000,000 parts from suppliers worldwide. The smaller parts are constructed individually before final assembly. Aligning all suppliers so that deliveries are made just-in-time and just-in-sequence is still one of the major challenges for large aircraft manufacturers.
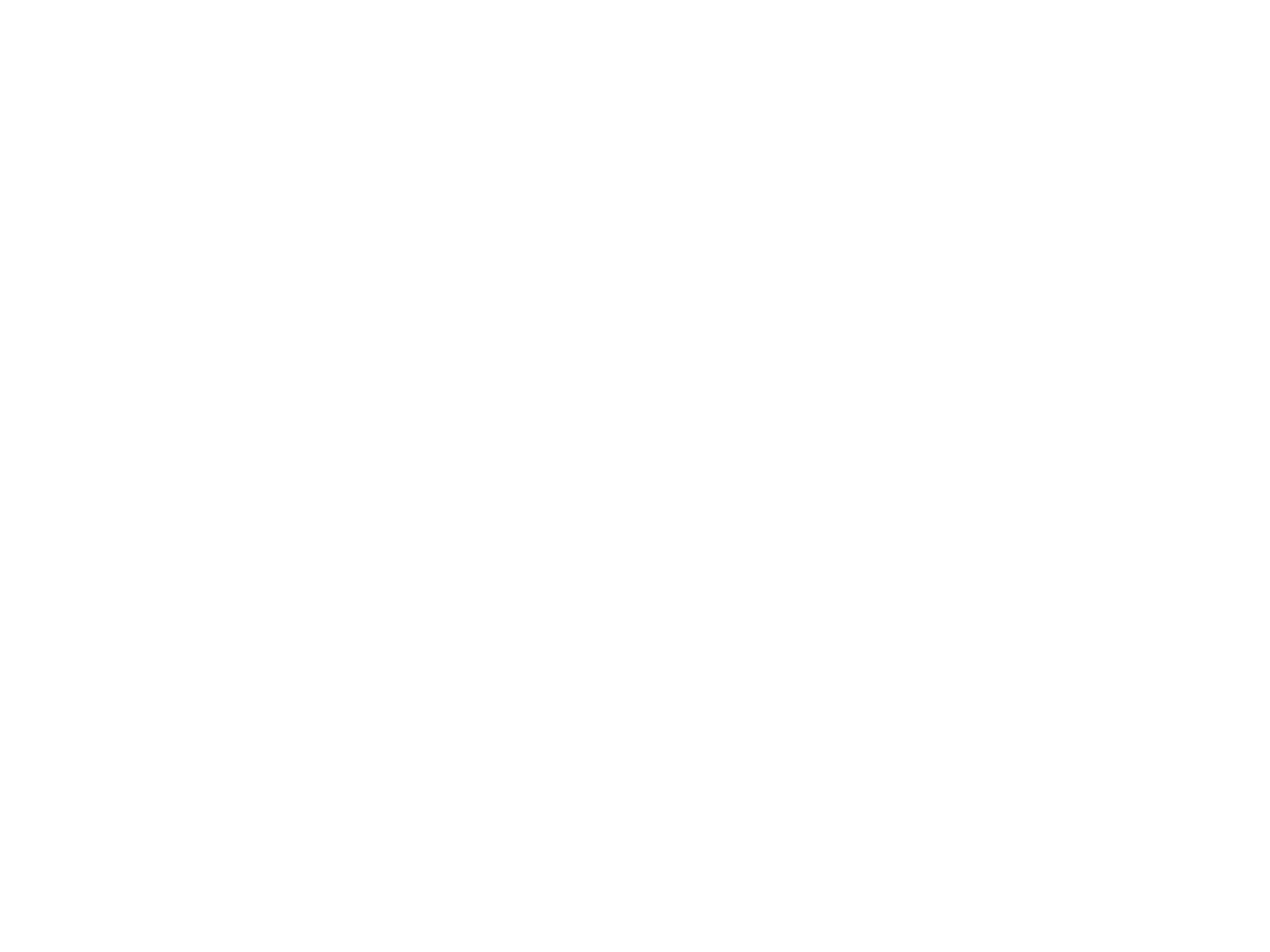
Our customers benefit from our digital supply chain management services. Each client has different needs, so we create tailored supply chain control tower solutions to connect all the dots along their value chain. This results in reduced logistic costs, optimized inventory, and secure worldwide supply.
Find out moreMaterials
Did you know that most modern aircraft consist of 50% aluminum?
Aluminum offers corrosion resistance and a high strength-to-weight ratio. This makes it easier for aircraft to reach a flight speed of around 900km/h while keeping fuel consumption low.
At thyssenkrupp Aerospace, our objectives are always to maximize quality and minimize scrap in all our processing services. By using smart processes such as nesting, we aim to keep your costs low, the quality of our materials high, and environmental impacts as low as possible.
Find out more Processing Services
Did you know that only around 15% of the materials acquired to manufacture an aircraft are actually used?
The so-called buy-to-fly ratio indicates the ratio between material inputs and outputs. In the aerospace industry, the majority of the materials acquired to make an aircraft end up as scrap. This is the result of inefficient processes along the supply chain and poor forecasting.
At thyssenkrupp Aerospace, our objectives are always to maximize quality and minimize scrap in all our processing services. By using smart processes such as nesting, we aim to keep your costs low, the quality of our materials high, and environmental impacts as low as possible.
Find out more Machining
Did you know that most narrow-body aircraft have a life span of around 40 years?
The aerospace industry works to the highest standards when it comes to processed materials. These materials operate under extreme conditions so the tolerances used in their manufacture are more precise than in almost any other industry.
Our customers save time and effort by putting the pre-machining of their materials into our expert hands. We work to highest engineering standards and use state-of-the-art machines. By focusing on their core business and leaving processing services to us, our customers stay competitive in their core business.
Find out more Supply Chain Management
Did you know that parts from around 2,000 suppliers are used to produce a narrow-body aircraft?
A large airplane consists of up to 6,000,000 parts from suppliers worldwide. The smaller parts are constructed individually before final assembly. Aligning all suppliers so that deliveries are made just-in-time and just-in-sequence is still one of the major challenges for large aircraft manufacturers.
Our customers benefit from our digital supply chain management services. Each client has different needs, so we create tailored supply chain control tower solutions to connect all the dots along their value chain. This results in reduced logistic costs, optimized inventory, and secure worldwide supply.
Find out more 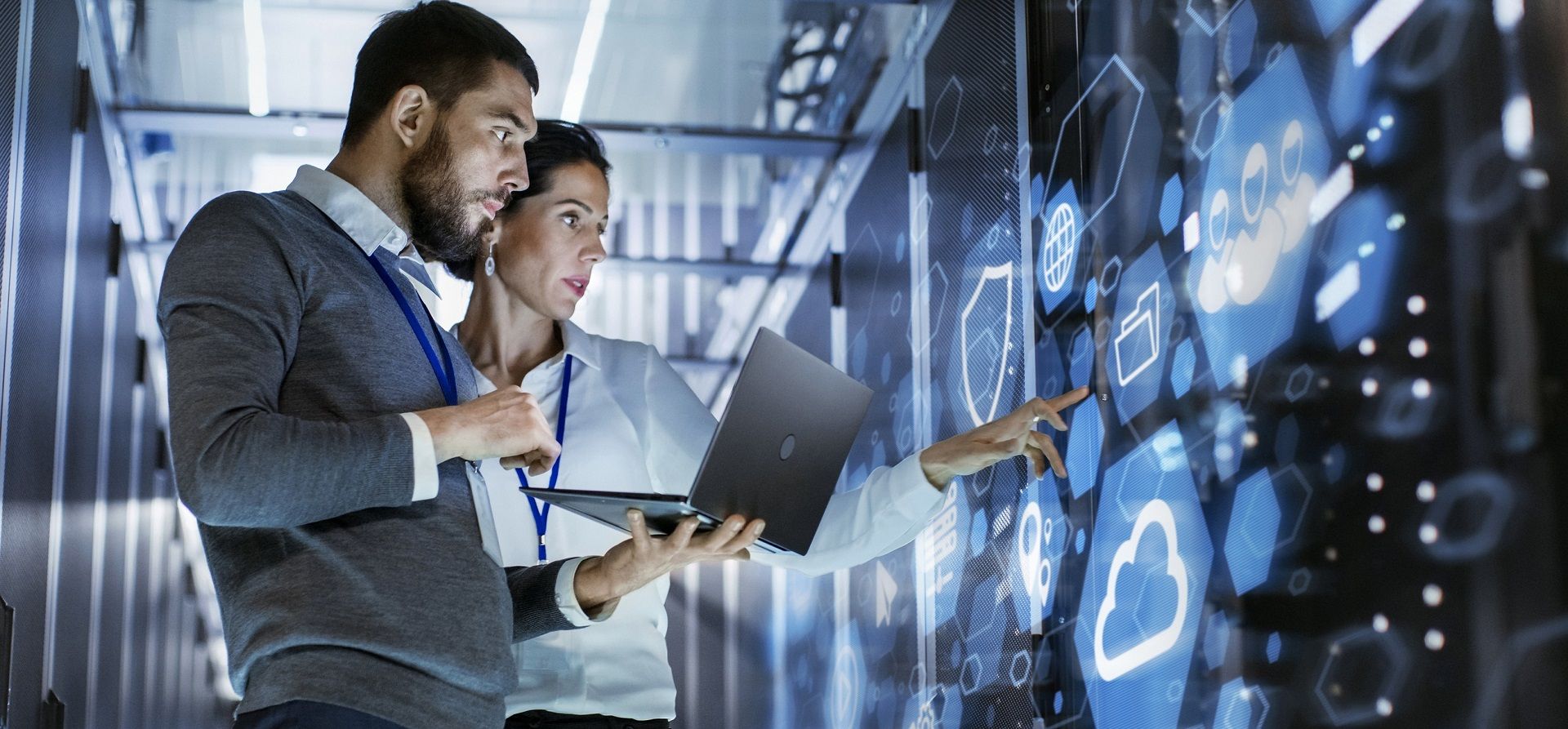
We are here to support you. Are you looking for a specific metal or need support to design your supply chain? Get in touch with one of our experts and get started today.
Contact our expertsWelcome to thyssenkrupp Aerospace